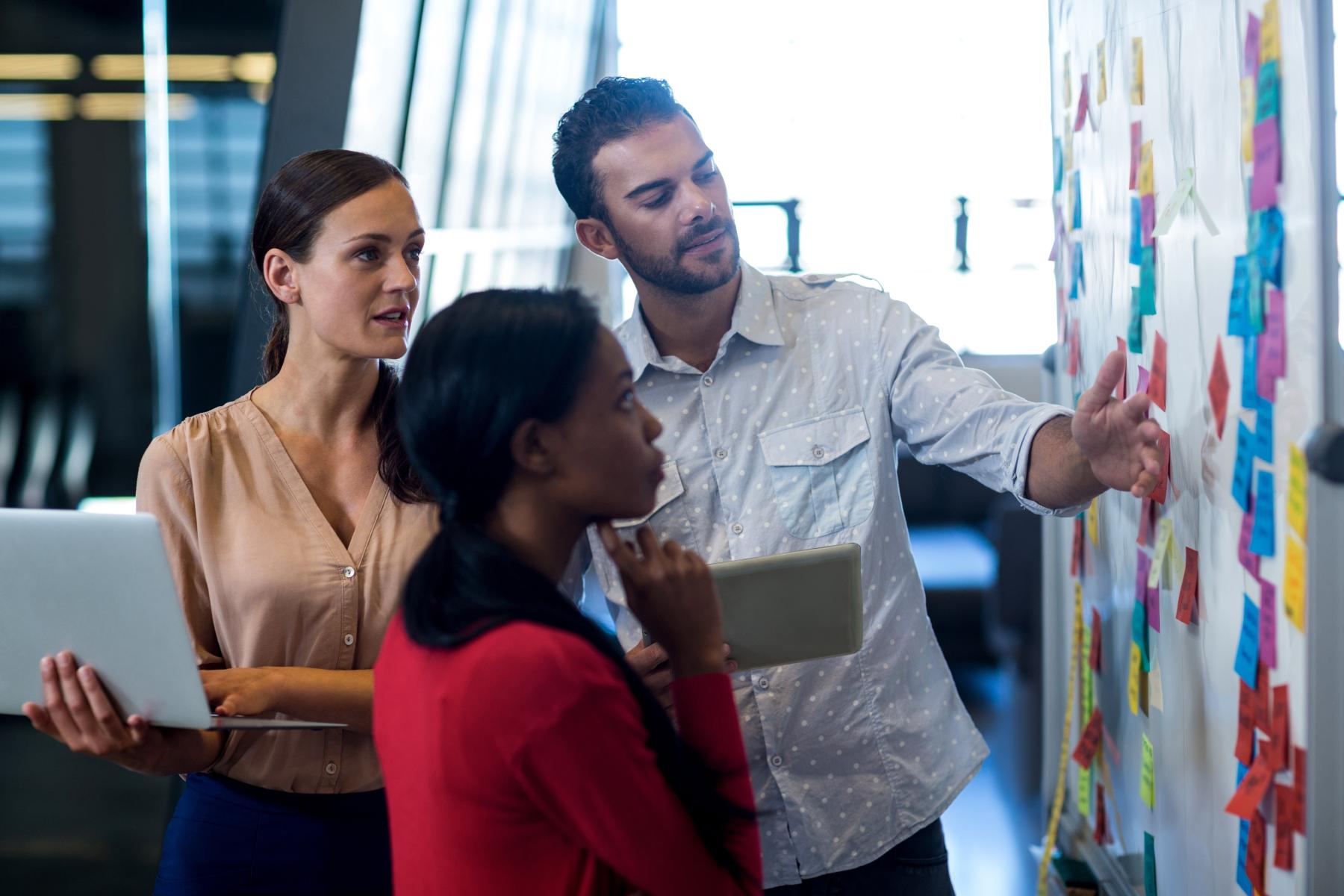
A Lean, Mean, Process Machine
Imagine a box of beads. Hundreds of beads. The beads appear to be the same size, and most of them are white, but a few are red. Using a special tool, we must try and extract only white beads from the box. In fact, our “job” depends on it.
This was a task we were assigned in a Lean Six Sigma class I am taking this summer. There were five of us selected to pull beads from the box, and we found that most of us were not very good at it. All of us got red beads mixed in with the desired white beads when we made our attempts. Yet, some of us were made team leaders, some were promoted, and others were… relieved of our duties.
When the activity was complete, we learned that there was absolutely no skill involved with using the tool to grab beads. In fact, it was completely random. If by chance you got all white beads, it was totally by luck.
How does this relate to our work as postdocs? Your lab is an organization. It has personalities, tasks, and obstacles. In order to produce better results, we have to find ways to be more efficient. For some of us, we simply have a lot of red beads in our box. Our red beads might be that one knucklehead undergrad who also works in our lab, or it might be the difficulty level of the research we are doing, or it might even be the P.I. that we are working for. Like the box of beads, sometimes we can’t control certain parts of the process. However, using tools like the ones in Lean Six Sigma can help us reduce waste or error and identify places where we can streamline.
Here are three coolest management tools I have learned this summer.
The Affinity Diagram
Most of us have done this one, but maybe it’s been awhile. This is the process where you brainstorm ideas and write them on a sticky note, and put them on the wall, then group them according to topic areas.
For example, what if I asked you to brainstorm all the ways we could make your experience at ASU as a postdoc better. The trick is to remember to put only one idea on each sticky-note. Then we might group them into categories of “easy to implement,” “needs higher authority to implement” and “very difficult to implement.” This would be a great way prioritize and attack the different ideas we want to try to implement.
What are some ways you could implement an Affinity Diagram activity in your lab? Tweet your ideas to @asupostdocs - #affinity
Process Mapping
Process mapping is an exercise where a manager draws a flowchart of a particular process that already exists, for the purpose of eliminating wasted time or procedures. The process map reveals where there are decision points that are repetitive, or where work-in-progress (wait time) is excessive.
To demonstrate this, I made a process map to try to streamline the task of scheduling a speaker for a Lunch ‘n Learn,. Scheduling guest speakers and coordinating schedules is the most difficult part of the process.
Having mapped the process, I can brainstorm ideas about how to make this process less of a hassle. In this case, there is repetition in learning if the candidate is interested and then finding a time when they are available. I can eliminate that wait time, and the repetitive questioning process, by consolidating that into one step.
Similarly, when I only offer one date at a time, I get caught in a cycle of the speaker not being available, and having to offer a new date. If I offer multiple dates at one time, or better yet, I just share a google sheet with the available dates on it, I can eliminate a lot of emailing back-and-forth.
The Process Map helps me visualize where the redundancies occur.
The 5S Method
The 5S Method is a “Lean” method for streamlining processes in a workspace or lab.
The 5 S’s are:
- Sort – decide what you need and remove unnecessary clutter
- Set in Order – Organize and arrange needed items so they can be located easily
- Shine – clean the area and equipment so everything looks and works like new
- Standardize – create a process for sort, set, and shine and maintain it
- Sustain – Audit the work area and track performance
Seems pretty simple, but something as easy as putting the 5S Method on a poster and hanging in your lab could help you keep your sanity.
And prevent the red beads from taking over your bowl.
- Wiley